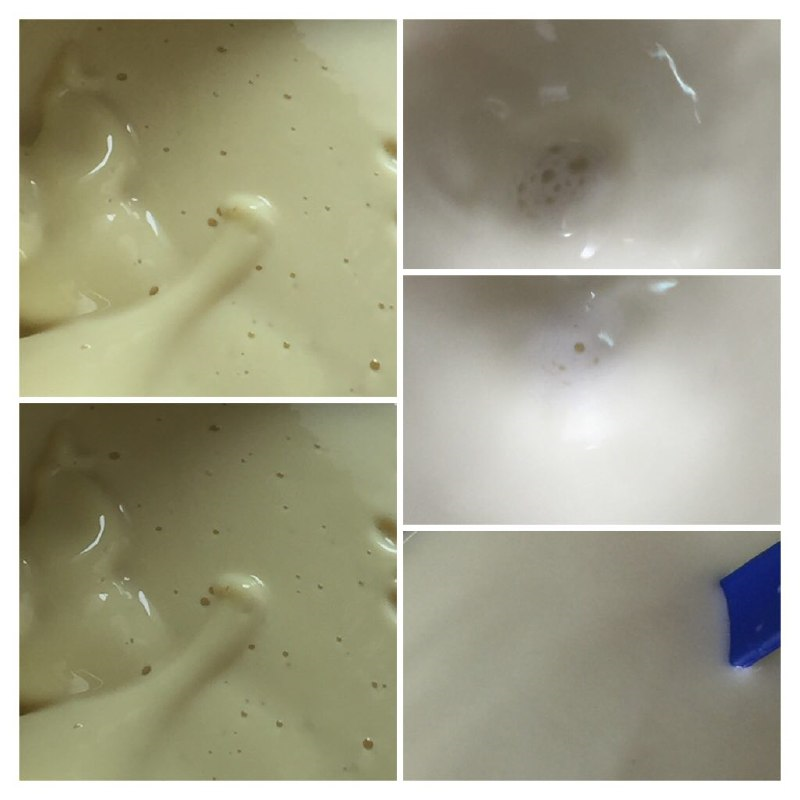
wax emulsion and/or in more general terms, wax emulsions are products which enable the application of the excellent barrier and protective properties of different kind of waxes in a simple, economical manner. The ease of application of wax emulsions without the need to use heat and melt processes results in an increasingly wide range of applications in the industry and at home. Wax Emulsions are used to:
• Coat Paper, Bristol Board And Cardboard,
• Waterproof Chipboard,
• Waterproof Fibers, Ropes And Textiles,
• Protect Floors, Car Bodies And Furniture,
• Coat Fruits and Vegetables.
The coating and waterproofing process may be done at a wide range of pressures to guarantee excellent penetration of the wax into the material. Wax emulsions are of the oil in water type, with water being the dispersion phase and wax being the dispersed phase. Most often, these are paraffin wax and/or other types of waxes or substances containing petroleum waxes, such as paraffin wax and slack waxes.
Since waxes in general and in particular paraffin waxes are immiscible with water and are not wet table, the creation of paraffin wax emulsions is difficult, requiring the application of appropriate emulsifiers. The preparation mechanism of oil in water emulsions is well known. It is based on the theory of inter-phase surface tension and orientation theory, developed in the early 20th century.
Production technologies of wax emulsions were developed in the 1960’s and the 1970’s, mostly by trial and error.
In practice, wax emulsions are dispersions of a finely fragmented solid phase in water. It was established that in the presence of emulsifiers and with vigorous mixing, melted waxes disperse as semi-liquid or liquid droplets with a diameter of 20 to 40 micrometers. The size of the dispersed particles can be greatly reduced by an additional input of mechanical energy, such as mechanical homogenization or the breaking up of the particles by ultrasound. This impacts directly on the stability of the wax emulsions.
Currently, stable wax emulsions are made by the application of pressure which allows re-emulsifying liquid wax in the water phase.
Paraffin wax emulsion manufacturing methods
In general, there are three basic methods to manufacture wax emulsions:
• Dispersion Of Water In Wax
• Dispersion Of Wax In Water
• Pressure Emulsification
The water into wax method comprises the addition of hot water to melted wax containing emulsifiers and appropriate additives and vigorous mixing. As more water is added, the water in wax emulsion inverts into a wax in water emulsion. The method requires the application of waxes with a low melting point and a relatively low viscosity.
The wax into water method most often comprises the melting of wax with the addition of one emulsifier and adding the mixture to hot water, containing other emulsifiers and additives with vigorous mixing.
The wax is added directly on the surface or inside the water phase via an opening in the shaft of the mixing paddle.
There are two pressure emulsification techniques: direct and indirect. The direct method is used to make wax emulsions using non-ionic surfactants.
The method consists of mixing in a homogenization tank (homogenizer) of all waxes, emulsifiers, additives (anti-foaming and pH regulating agents) and water at a temperature 10 °C higher than the melting point of the wax and at a pressure of up to 200 atmospheres. The wax emulsion is then rapidly cooled at atmospheric pressure using an effective external heat exchanger.
The indirect method is used for all types of wax emulsions, and in particular for wax emulsions made using anionic and cationic surfactants.
The method consists of the formation of an initial wax emulsion containing all the wax components, surfactants and additives and part of the water. The remainder of the water is injected in controlled batches at a temperature of less than 100 °C. This results in the inversion of a water in wax emulsion into a wax in water emulsion.
The wax emulsion is then rapidly cooled under atmospheric pressure using an effective external heat exchanger.