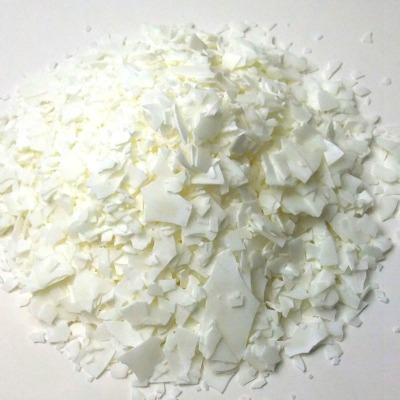
Production of candle is an art at the present time. There are so many candle waxes available in the market these days but selecting the right candle wax or blend of candle waxes in order to produce the right candle is very critical. In this article, we talk about candle wax and Additives
Candle wax for candle making
As mentioned above, type of candle wax fuel in the construction of candles changed during the past 200 years. Today the most commercial candle wax fuel available worldwide is paraffin wax. As the demand changes candle manufacturers forced to comply with the market forces in order to create stronger and high melting point candles. There are several commercial standards for candles. In the United States candles are required to have at least 60 percent paraffin wax.
Other additives such as stearic acid, carnauba wax can be mixed with paraffin wax to modify the softening and/or melting point of finished candle wax. Other candle wax types such as Beeswax and Soy wax are used by candle manufacturers to make natural candles, but they are become more expensive compare to candles made from paraffin wax. Wicks are needed to be made from high quality cotton or linen in order it burn in one direction.
Excluding the natural waxes, paraffin waxes both fully refined and semi refined grades are suitable for production of candles. It is notable that type of candle dictates the percentage of paraffin wax.
For instance, Votive or Container candles requires a specific blend of paraffin wax and other candle waxes but, if the manufacturer need greater than 4% fragrance may require addition of additives. Further, Mottling Container candles also needs a design of specific paraffin wax blend containing no additives which must be pour between 180-195°F. It is notable in preparing the paraffin wax and/or candle wax base higher fragrance levels yield better mottling, but levels above 6% may result in surface oil.
Additives for candle wax
Additives also play a key role in manufacturing of candles. These additives must be complying with the paraffin wax and/or candle wax base in order to make the required candle. Below paragraphs explains the overall application of common additives widely used in candle manufacturing industry.
Ethyl Vinyl Acetate is used to impart hardness and strength to a candle. This additive is typically used to strengthen dipped taper candles. It is not recommended for molded candles since it tends to cause the candle wax base to adhere to metal molds. EVA is a rubbery plastic like material that takes time to blend into a candle wax. EVA will prevent mottling. Use is typically limited to less than 4%.
Microcrystalline Wax is used for fragrance holdout. This will help prevent “wet spots” in container candles when a high concentration of fragrance is used and will prevent mottling. Use should be limited to 2% or less. Higher concentrations may hinder fragrance release.
Beeswax Substitute used as a low cost substitute for beeswax .Beeswax Substitute can be added to paraffin wax and/or candle wax base to increase its melting point, which will lengthen the burn time of a candle. The addition of too much Beeswax Substitute can add to excessive soot formation.
Mineral Oil used to aid adhesion of the candle wax base to the container or to lower the melting point of a candle wax blend. Usually a 6-8 % mineral oil / fragrance combination is ideal for candle wax adhesion to the container. Excessive use will generate soot when the candle is burned. Mineral Oil helps promote mottling in candle waxes designed to do so.
White Petrolatum used to aid adhesion of the candle wax to the container or to lower the melting point of a candle wax blend. Petrolatum will add a creamy look to a container candle. Excessive use will generate soot when the candle is burned.
Polyethylene Wax is used to add a glossy surface to pillar, votive, and other molded candles. This will increase candle hardness and will affect the candle burn rate. A larger than typical wick is usually necessary when using Polyethylene Wax as an additive. Addition will also help with color distribution. Polyethylene Wax will prevent mottling. Use should be limited to less than 2%.
Addition of Stearic Acid will add opacity to candles. Stearic Acid will also harden the candle wax and acts as an internal mold release for molded candles. Typical concentrations are up to 10%. At high concentrations, Stearic Acid may contribute to color fading and discoloration. Stearic Acid may be used to control the amount of mottling. Concentrations greater than 10% will typically prevent mottling.
Adding approximately half percentage may also help in fragrance release when a candle is solid. Stearic Acid will also aid in fragrance holdout for container candles. Excessive use will generate soot when the candle is burned.
Vybar 260 used to aid in even color distribution. Vybar 260 also increases the hardness of a candle wax. Adding approximately half percentage may help in fragrance release when a candle is solid and will prevent mottling. Typical usage is up to 4%.