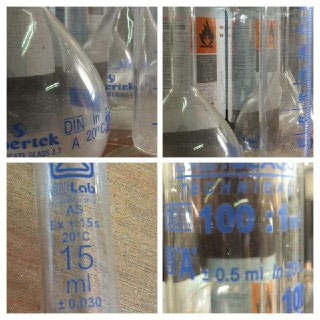
Drilling fluid are used to aid the drilling of boreholes into the earth. The application of drilling could be to extract oil and gas from beneath the earth or simply drilling water well. There are three main categories of drilling fluid. Water based fluid , oil based and synthetic based drilling fluid.
Each of these drilling fluids has its own advantages and disadvantages, however, three key factors usually determine the type of drilling fluid selected for a specific well are:
• Cost of drilling fluids
• Technical Performance
• Environmental Impact
Water based are used worldwide. Depending on the projected well conditions base fluid may be fresh water, seawater, brine, saturated brine, or formate brine. Water based are fall in to two categories; nondispersed drilling fluid and dispersed drilling fluids. Water based are most preferred worldwide due to its low cost compare to the two other categories as well as its low environmental impact. Water based limitations are as follow:
• Formation Clays That React, Swell, Or Slough After Exposure To WBFs
• Increasing Downhole Temperatures
• Contaminants
• Stuck Pipe And Torque And Drag
These limitations of Water based in 1950-1960 lead to creation of oil based drilling fluids to address these critical issues. Oil based in use today are formulated with diesel, mineral oil, or low-toxicity linear olefins and paraffin. As the demand for oil and gas grow hence, more drilling resulted in arising environmental issues worldwide.
As a result, Synthetic-based drilling fluids were developed out of an increasing desire to reduce the environmental impact of offshore drilling operations, but without sacrificing the cost-effectiveness of oil-based systems.
What to expect from drilling fluid in oil and gas industry
Once the drilling begins, removing cuttings and material from the borehole become an issue. Drilling fluids must carry the drilled material to the ground surface either by viscosity or velocity. Further, as drilling continues drill bit temperature is raising because of friction generated during the drilling process.
Thereby, drilling fluids need to pass by the drill bit and must have the capacity to absorb heat and carry the same up the borehole.
During the drilling of well, as time passes material and cuttings will stick to drill bits such as clay particles. This phenomenon will result in inefficiency in drilling and waste of time and money. Therefore, cleaning the drill bit is vital. Drilling fluids exits the bit jets, the fluid’s velocity removes material from the bit teeth and the cuttings from the bit formation interface. This prevents the re-cut or re-ground.
As mentioned above, as the time passes cuttings, clays and other material will deposited on the borehole wall. This will result in creation and formation of a barrier. Once the barrier forms it will limit the amount of drilling fluid which can penetrate the formation.
In oil and gas field this phenomenon known as filter cake. Filter cake is vital factor of drilling fluid as it is directly linked to the formation stability and additionally, well development time is reduced if drilling fluid loss to the formation is limited and controlled.
Another aspect of drilling fluids is its ability to prevent borehole from collapsing. This can be achieved by increasing the Drilling Fluids weight to surpass the formation pressure. Finally, drilling fluid gel strength must be at a level to keep the cuttings and drilled material in suspension form if there is lack of drilling fluids velocity.