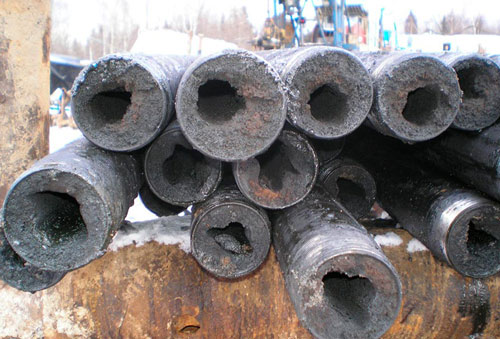
In production of oil and gas each well drilled contain crude which has paraffin waxes dissolved within and under appropriate environmental conditions can deposit over time. These paraffin waxy deposits can build up in production equipment and pipelines, potentially restricting flow (reducing volume produced) and creating other problems.
Paraffin Wax in crude oil
There are two categories of paraffin waxes in crude oil Macrocrystalline wax and Microcrystalline wax. Macrocrystalline waxes are long chain carbons of C18 to C75+, having individual melting points from 40 to 70°C. Microcrystalline waxes are referred to Naphthenic hydrocarbons (C18 to C36). Macrocrystalline waxes lead to paraffin wax problems in production and transport operations; microcrystalline waxes contribute the most to tank-bottom sludge’s.
As mentioned above each well drilled has its own crude which has unique properties. Even geographical position of well affect the properties of crude in a drilled well.
Some wells do have clean paraffin waxy crude which is mainly consist of hydrocarbons and paraffin wax as the heavy organic constituents and some might be regular paraffin waxy crudes which contain other heavy organics in addition to the paraffin waxes. Other hydrocarbons can be asphaltenes and resins.
Interaction of these heavy organics in crude oil and nature of crude oil either heavy and/or light can end up either prevent paraffin wax-crystal formation or enhance it. It is notable that up to the present time this interaction caused the most severe problem in oil and gas industry worldwide.
How paraffin wax deposits
Temperature of crude plays a key role in paraffin wax deposits. As temperature drops the below critical level, paraffin waxes begin to form insoluble crystals. Further, interaction of asphaltenes, resins and inorganic solids forms paraffin wax deposits. Paraffin wax deposits can also contain other materials such as Gums, fine sand, Silt, Clays, Salt and water. Paraffin Wax deposits vary in consistency from a soft mush to a hard, brittle material.
Paraffin wax deposits will be harder, if longer-chain n-paraffins are present. High-molecular-weight paraffin waxes tend to deposit in the higher-temperature sections of a well, while lower-molecular-weight paraffin wax fractions tend to deposit in lower-temperature regions.
Prior to solidification, the solid paraffin wax crystals in the liquid oil change the flow properties from a Newtonian low viscosity fluid to a very-complex-flow behavior gel with a yield stress.
Coping with paraffin wax deposits
As of today, there are three popular methods which one can cope with paraffin wax deposits. Prevention and/or inhibition, Crystal modifier and Dispersants and removal of paraffin waxy deposits are the most effective methods used widely in oil and gas industry.
Prevention can be more cost effective than removal. One key to paraffin wax deposition prevention is heat. In this process crude oil temperature needs to be raised. Electrical heaters can be employed to raise the crude oil temperature. There is couple of limitations attached to this process.
First is the maintenance cost of heating system and the availability of electrical power. Second, high well temperature will lead to higher flow rates and increase the shearing action of the flowing fluid.
paraffin wax deposition can be prevented, delayed, or minimized by the use of dispersants or crystal modifiers. As with asphaltenes, paraffin wax characteristics vary from well to well. Chemicals that are effective in one system are not always successful in others, even for wells within the same reservoir.
For this reason it is of fundamental importance to establish a good correlation between oil composition and paraffin wax inhibitors efficiency, leading to an adequate product selection for each particular case, avoiding extremely expensive and inefficient trial and error procedures. Types of paraffin wax-crystal modifiers include: Maleic acid esters, Polymeric acrylate and methacrylate esters, Ethylene vinyl acetate polymers and copolymers
Dispersants are material or in specific surfactants which keep the pipe surface wet in order to minimize the tendency of the paraffin wax to adhere. This act will result in to keep the paraffin wax particles bonding. Limitations of this technique are maintaining high level of water in the system. High level of water might decrease the temperature of well and/or pipeline and various forms of erosion are highly detrimental.
Another popular method is removal of paraffin waxy deposits. This can be done by Cutting, Drilling, and Chemical dissolution, melting by the use of hot oil, hot water, or steam. The use of hot oil has been the most popular, normally pumped down the casing and up the tubular. It is intended that the high temperature of the liquid phase heat and melt the paraffin wax, which then dissolves in the oil phase. Using the bottom-up delivery approach, hot oil first reaches those paraffin waxes most difficult to melt. The higher in the tubular the hot oil proceeds, the lower its temperature becomes, thereby reducing its paraffin wax-carrying capacity.
Hot oiling can cause permeability damage, if the fluid containing the melted paraffin wax enters the formation. Hot water, hot-water/surfactant combinations, and steam are alternatives to hot oiling. Plain hot-water treatments do not provide the solvency required to remove the paraffin wax, hence the use of surfactants to disperse the paraffin wax. The advantage of water is its greater heat capacity. Various aromatic solvents can be used to dissolve the paraffin wax.
These are generally not heated, relying solely on the solvency properties of the fluid. As with asphaltenes dissolution, o-xylene has been one of the more effective solvents for paraffin waxes. Kerosene and diesel tend to be poor solvents. However, as with asphaltenes dissolution, one solvent does not necessarily work equally well on all paraffin wax deposits.
Pigging is the primary mechanical method of removing paraffin wax buildup from the internal walls of pipelines. The pig cuts the paraffin wax from the pipe walls; a bypass can be set with a variable-flow pass, allowing the pig to prevent paraffin wax buildup in front.
Pig sizing can vary, and multiple pig runs with pigs of increasing size can be used. For subsea pigging, a looped flow line is required or a subsea pig launcher for a single flow line. The major uncertainty in this operation is the paraffin wax hardness as it is formed in the pipeline.
Coiled tubing with the appropriate cutters at the end also can be used for paraffin wax removal—the drawback for pipeline cleaning being the limited reach of the coiled tubing. For wellbore cleaning this is obviously less of a problem.